O Ring Slot Dimensions
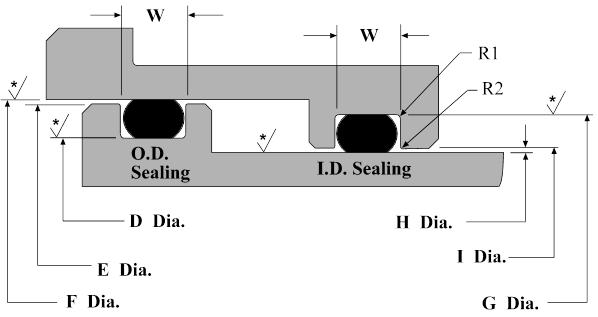
O Ring Slot Dimensions Calculator
DESIGN DIMENSIONS FOR O-RING INSTALLATION O-rings are normally used as seals in several ways, and dimensions of the groove or gland will also vary with the cross section of the ring, the type of operation, and the amount of pressure used in the system. These dimensions will also be different if the O-ring is sealing a liquid which has a low volume. O-rings are available in various metric and inch standard sizes. Sizes are specified by the inside diameter and the cross section diameter (thickness). In the US the most common standard inch sizes are per SAE AS568C specification (e.g.
O-ring groove design guides offer default dimensional guidance on the most basic o-ring groove design applications. The best o-rings are useless without the right groove design which becomes increasingly important the more demanding the application environment. Review the general o-ring groove design considerations before moving onto the specific o-ring gland design type.
O-ring Groove Dimensions Static


O-ring Groove Dimensions Parker
Ideal design: r > 6 x W diameter but no less than r > 3 x W diameter
To minimize installation difficulties arising from stretch or OD compression on the seal, the centerline perimeter of the groove should match the centerline circumference of the O-ring. The rectangular cross section of the groove will follow the suggested guidelines in the O-Ring Handbook.
For those times when hardware real estate is at a premium and we simply cannot increase the inside corner radii to the desired size, an alternative option is the O-Seal. The O-Seal has a round cross section like an O-ring. However the footprint of the O-Seal is designed to match the shape of the groove. The primary advantage of the O-Seal is custom molding to fit the exact groove, eliminating the concern that comes with bending stress at the corners. A smaller corner radii can be used for the groove, allowing the footprint to fit perfectly within the application’s design constraints.
If there are multiple ports or openings on the face, or bolt holes to contour around, these seals can be consolidated into a single O-seal solution. By consolidating seals, the installation process becomes much easier. All seals are ready to be installed at the same time, and the risk of installing the incorrect seal material is eliminated. This may offer the added advantage of streamlining the bill of materials and simplifying the amount of stock to be replenished during the assembly process.
O-Seals are available in nearly every material family and engineered for optimum size and configuration for each unique application. Parker Application Engineers are happy to assist you with your racetrack groove design or a custom O-Seal. Please contact us today via online chat or by email by visiting Parker O-Ring and Engineered Seals Division website.
This article was contributed by Dorothy Kern , applications engineer lead, O-Ring & Engineered Seals Division
Related content: